Phase Shift of Ferrous Material
Deep Dry Cryogenic Treatment (DDCT) improves the mechanical properties of steel by promoting the transformation of retained austenite into martensite—a much harder and more stable phase. In conventional heat treatment processes, such as austenitizing followed by quenching, not all austenite transforms into martensite. This is especially true in high-carbon and alloyed steels where some amount of austenite remains stable at room temperature. This retained austenite is relatively soft, and its presence can reduce dimensional stability, wear resistance, and overall hardness of the component.
The transformation from austenite to martensite is thermally activated and begins at what is known as the martensite start temperature (Ms) and continues until the martensite finish temperature (Mf). While the Ms temperature for many steels is above room temperature, the Mf temperature can be significantly lower—often below -50-100°C. Standard quenching methods do not reach low enough temperatures to complete the transformation, leaving a significant portion of retained austenite.
DCT addresses this limitation by exposing components to extremely low temperatures, typically between -160°C and -190°C, using liquid nitrogen. Holding the material at these temperatures for 8 to 36 hours ensures that the retained austenite transforms fully into martensite. This deep cooling process must be carefully controlled to avoid thermal shock and minimize the development of internal stresses.
The result of this complete transformation is a microstructure with a much higher proportion of martensite, leading to increased hardness, enhanced wear resistance, and improved dimensional stability. These benefits make DCT especially valuable for tools, dies, gears, and other high-performance components subjected to extreme conditions.
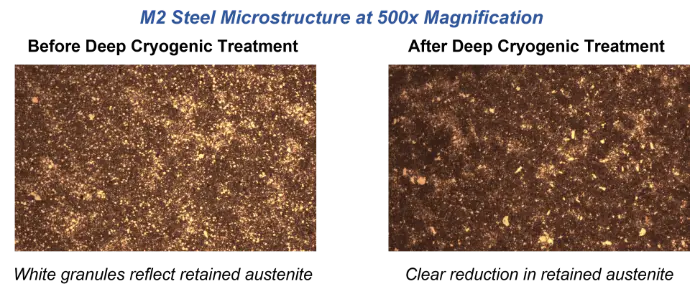
Promotes Eta (η) Carbide Precipitation
Deep Dry Cryogenic Treatment (DDCT) doesn’t just finish the martensitic transformation—it drives the precipitation of ultra-fine η (eta) carbides within the microstructure. When steels or cemented carbides are held at –160 °C to –190 °C for many hours, carbon atoms become highly mobile, clustering into nanoscale carbides—typically 3 – 10 nm in diameter—uniformly dispersed throughout the matrix. Their density is far higher than what forms with conventional cold or room-temperature processing, giving the treated alloy a second, nano-level “skeleton.”
In high-carbon tools and high-speed steels, these particles are orthorhombic Fe₂C (η-carbide). Because they nucleate on dislocations and grain boundaries, they pin the movement of dislocations, inhibit grain growth, and act as extremely effective secondary-hardening sites during subsequent tempering. The result is a simultaneous rise in hardness, wear resistance, and temper-retention (hot-hardness) without a proportional increase in brittleness—one of the reasons cryo-treated dies and cutters often show double-digit gains in tool life.
In tungsten-carbide/cobalt composites, DCT can trigger a controlled precipitation of η-phase carbides such as Co₆W₆C along the cobalt binder channels. Far from the brittle, network-type eta phase that sintering engineers try to avoid, these discrete, nanometric precipitates refine the binder mean-free-path, lock WC grains in place, and raise both hardness and transverse-rupture strength. Taken together, the formation of finely dispersed η carbides is a core mechanism behind the dimensional stability, superior wear resistance, and extended service life observed in cryogenically processed steels and cemented carbides.
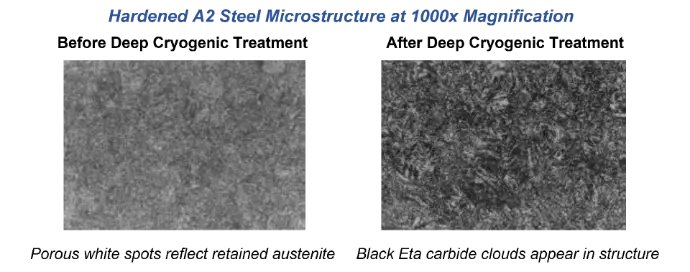
Relieves Internal Stresses
Deep Dry Cryogenic Treatment (DDCT) is highly effective in reducing internal residual stresses in metallic components, particularly in hydrogen-resistant steels. Residual stresses, often introduced during forging, machining, or welding, can cause undesirable distortion, dimensional instability, and even premature failure during service. Cryogenic treatment significantly alters the internal stress profile by transforming retained austenite into martensite and promoting a more homogeneous and stable microstructure.
The residual stress simulation profiles from studies show a stark contrast: prior to cryogenic treatment, the material exhibits high tensile stresses concentrated in the core (red zone), which are potentially harmful under mechanical or hydrogen-induced loading. Post-DCT, however, the same profile shifts to a more uniform compressive or low-magnitude stress distribution (green to light orange zones). This redistribution is critical because compressive residual stresses are known to suppress crack initiation and propagation, thereby enhancing fatigue resistance and operational safety.
The reduction of residual stress offers key benefits to all steel grades—from tool steels and high-speed steels to structural and stainless steels. Components become dimensionally more stable, especially under cyclic or thermal loading. Fatigue resistance and impact toughness are significantly improved due to the suppression of stress raisers. Moreover, parts show better machinability and surface finish, fewer in-service failures, and enhanced long-term performance. Whether in cutting tools, aerospace structures, molds, gears, or pipelines, the stress relief effect of DCT provides a robust foundation for reliable and durable steel components.
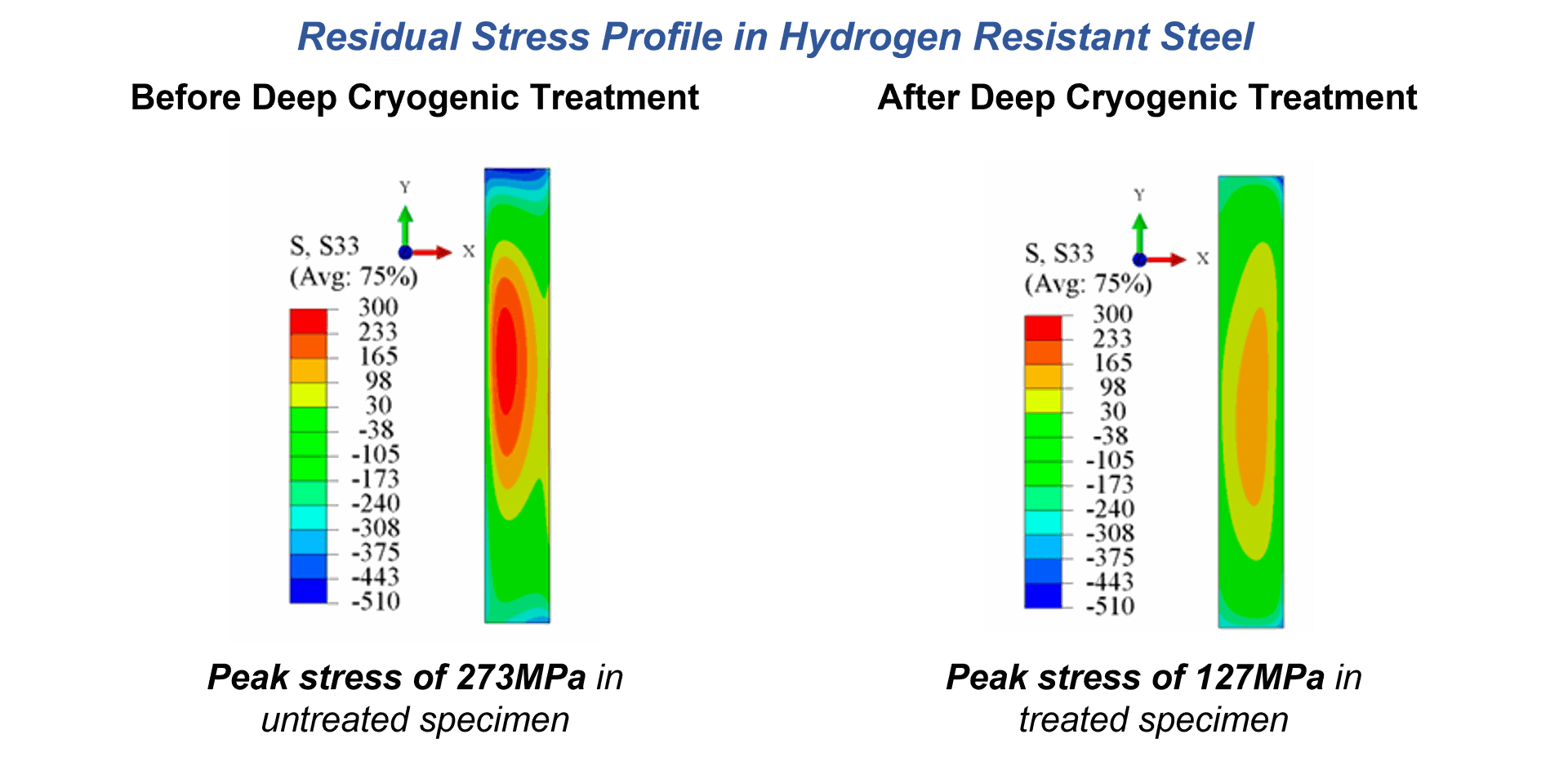
Refines & Densifies Microstructure
Deep Dry Cryogenic Treatment (DDCT) leads to a significant refinement and densification of the crystalline structure in metals, particularly steels and carbides. When materials are exposed to extremely low temperatures (typically –160 °C to –190 °C), the atomic lattice contracts uniformly, promoting a tighter atomic packing and encouraging the reordering of dislocated or distorted regions. This results in a more uniform and stable microstructure with fewer imperfections.
The visual representation reinforces this transformation clearly. On the left, the pre-treatment structure contains gaps, tears, and overlaps, indicative of lattice mismatches, grain boundary voids, and internal inconsistencies that weaken the metal’s performance. On the right, after cryogenic processing, the structure is uniform, dense, and orderly—a visual metaphor for how the crystalline grains realign into a more energetically favorable state. This improved grain alignment minimizes points of stress concentration and enhances load-bearing capability.
Such microstructural densification translates to tangible performance gains. DCT-treated materials demonstrate wear resistance, fatigue life, and dimensional stability, particularly in demanding applications like tooling, aerospace, and automotive components. The refined grain structure also improves thermal conductivity and resistance to crack initiation, making the material more resilient under both thermal and mechanical cyclic loading. In effect, DCT acts like a deep molecular reset—eliminating microstructural noise and instilling a new level of internal order and integrity.
Select benefits can be visualized in a consistent & reduced wear profile which can sizeably reduce regrinding frequency & costs:
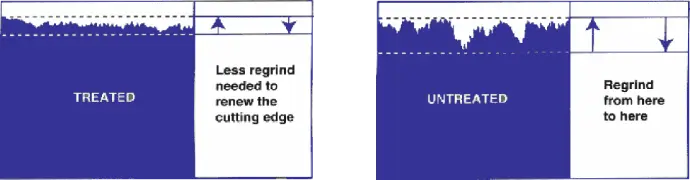